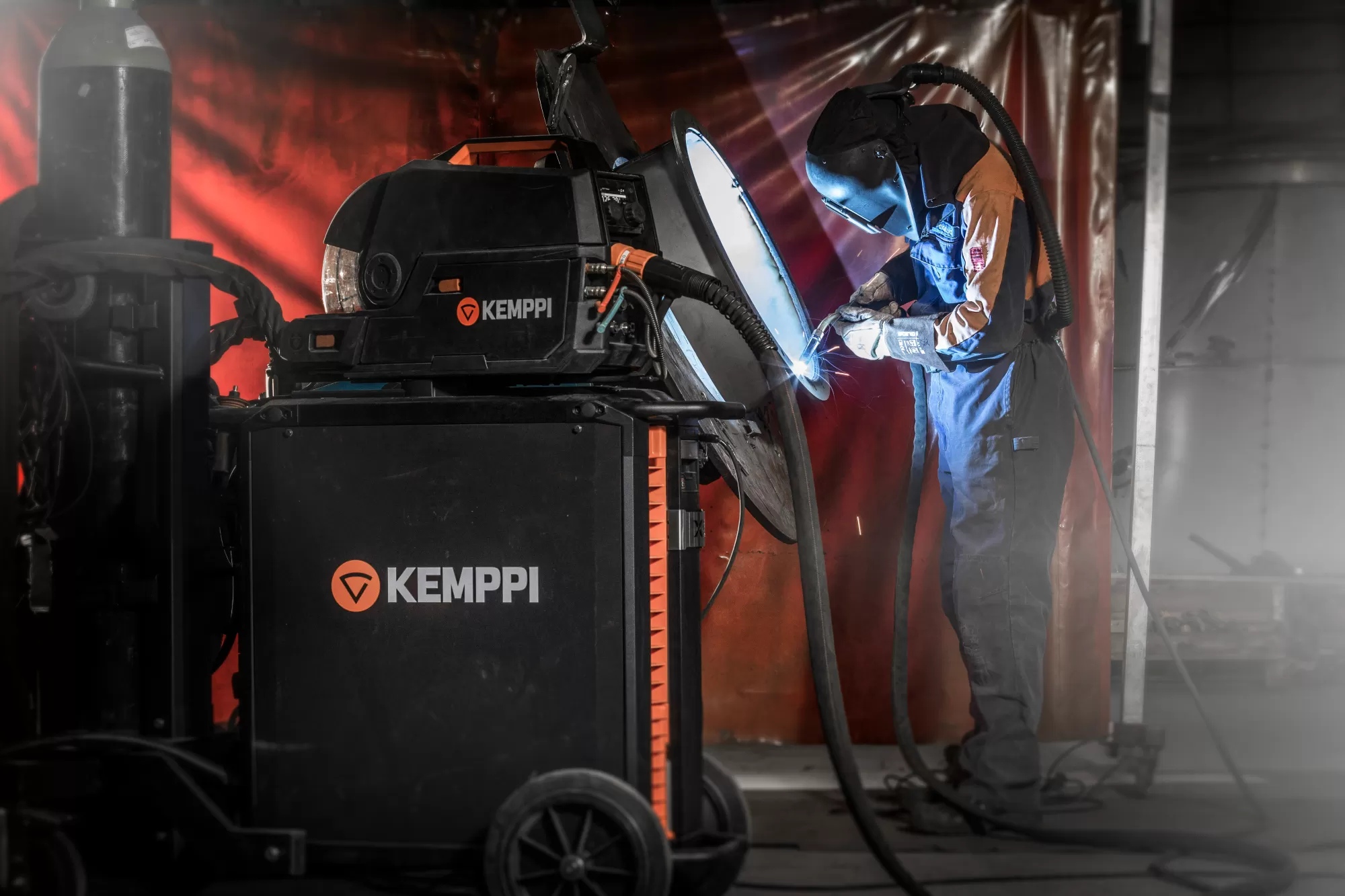
Mesekon
The expert of welded steel structures
Better ergonomics and adjustability with the X8 MIG Welder
Mesekon has been working closely with Kemppi in tackling the welding of challenging materials. Due to its better adjustability, the X8 MIG Welder facilitates the welding of wide-ranging materials and improves work ergonomics for the welders.
Founded in 1994, Mesekon is a contract manufacturer and a manufacturing technology consultant for leading export companies in the technology industries. The company’s key strength is its welding expertise related to machine manufacturing. Its customers include manufacturers of engines and turbines, offshore and shipbuilding equipment, pulp and paper machines, lifting and handling equipment, and mining, quarrying and construction machinery. The company has altogether 50 employees in Turku and Mynämäki, Finland. The Turku site focuses on stainless steels and the Mynämäki site on carbon steel.Mesekon constantly develops the design and manufacturability of its main products: components and complete assemblies for offshore equipment, wet scrubbers and man lift booms. In terms of its competition, Mesekon stands out with excellent production quality, keeping up with the latest development of welding processes and equipment, and investing in own development and utilizing new production methods.
Main challenge
Development Manager, IWE Tero Nättiaho says that the company's 35 welders face an exceptionally wide range of materials: different structural steels, high and ultrahigh-strength steels, as well as highly alloyed steels, which all have their special requirements from the weldability point of view. The other key challenge is that there are about 1000 standards to comply with. The standards together with the vast material spectrum make project management really demanding. In the current market situation in which competition is extremely hard, it is also essential for a company to have good documentation management and the ability to qualify welding to different standardization systems.
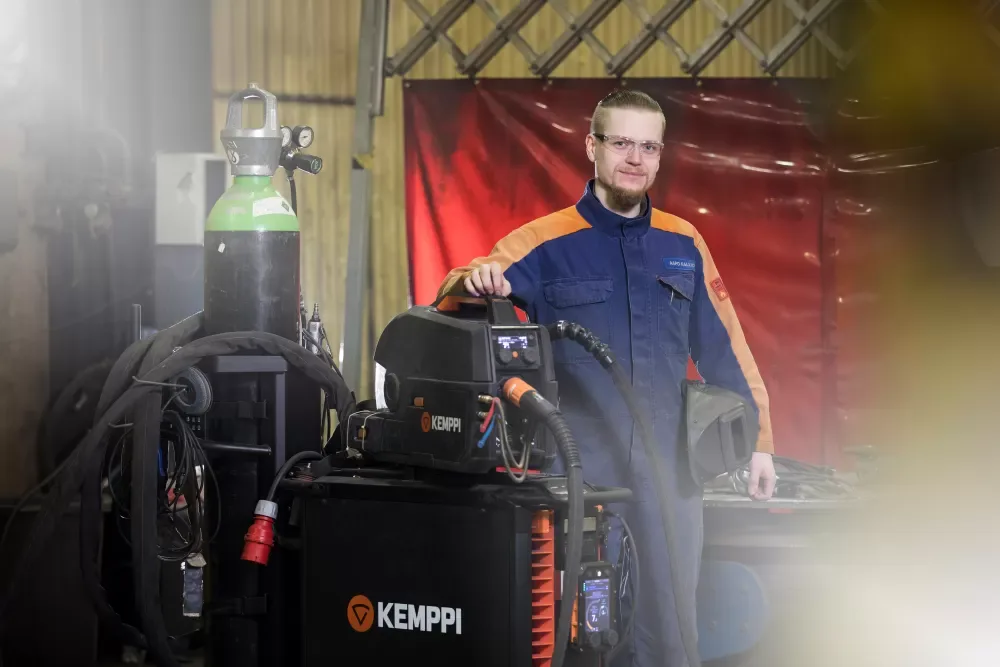
According to welder Aapo Kallio, the key strengths of the X8 MIG Welder are good usability and easy set up.
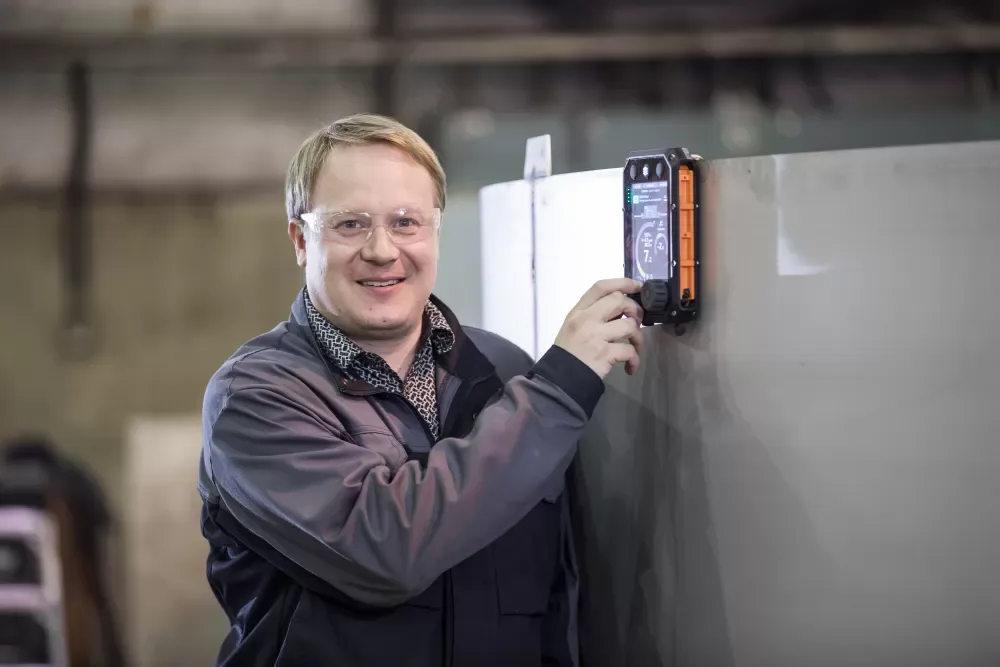
"The Control Pad is the future and a natural tool for new young welders," Development Manager, IWE Tero Nättiaho states.
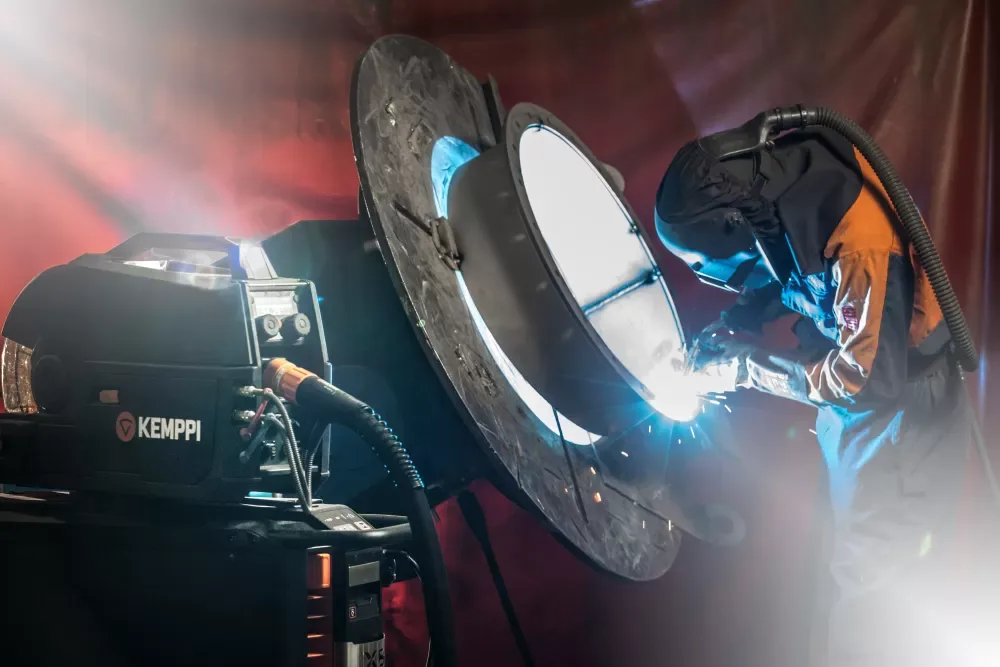
Mesekon's 35 welders face an exceptionally wide range of materials in their work.
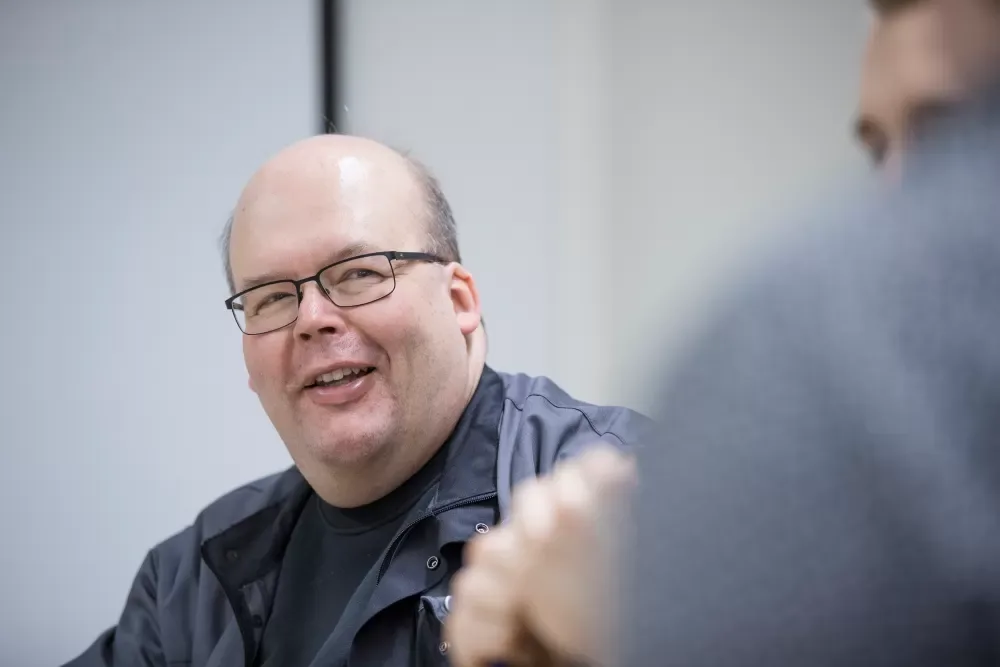
Production Manager, IWE Juha Sundell says that the X8 MIG Welder has lived up to all expectations.
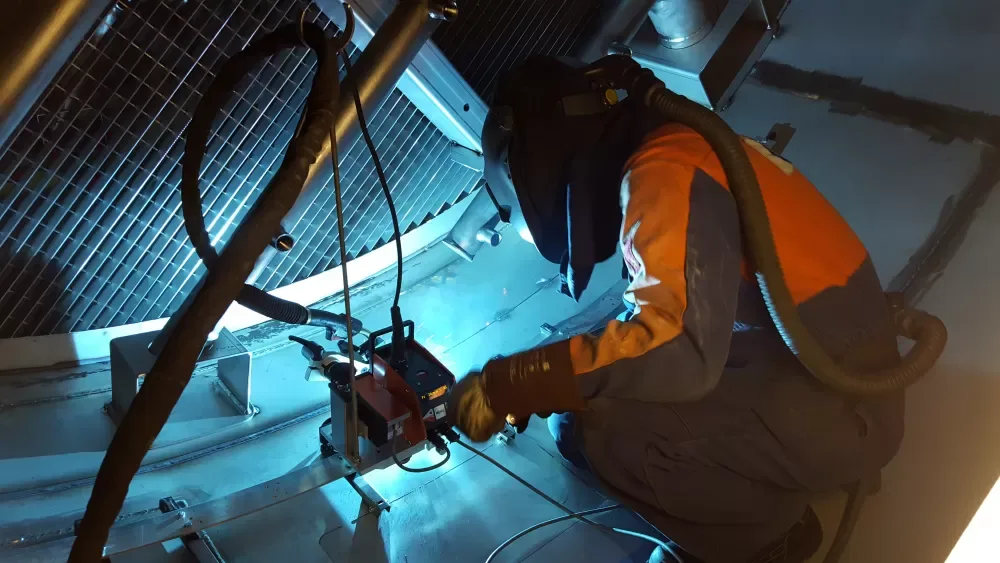
A part of the welding is carried out with mechanized welding equipment.
Kemppi's solution
Mesekon’s MIG/MAG and TIG welding equipment are all made by Kemppi. Plasma welding and the SAW process are also in use. Machines have been purchased when needed, usually investing in the latest technology. The company is following a one-stop shop approach for welding machines, as it makes life easier. It has also made the cooperation with Kemppi a close one. By working together, Kemppi has helped Mesekon to find solutions for controlling the weldability of the new materials that the company faces.
In spring 2017 Mesekon got Kemppi’s X8 MIG Welder for pilot use at their workshop, and the welders’ feedback has been very positive. They have especially liked the good usability of the machine and easy set up: the new wireless user interface, Control Pad, enhances comfort and ergonomics and thus improves also the welding quality.
“With the Control Pad, there's no need for squatting in front of the welding machine - you can just grab it and bring it to where you work, even inside the weld structure – and do there the adjustments needed from there.”, welder Aapo Kallio says. “Since having it, I have felt no need to make any adjustments on the wire feeder’s panel. And I really don’t want to go back to the old system." The new wire-changing features, and the welding gun’s pistol grip handle and work light got positive comments too.
Mesekon was also impressed by the X8 MIG Welder’s improved welding properties. For Mesekon, the increased data transfer rate of the welding machine is important, because it enables better control of the machine – a very important equipment feature when working with challenging materials. Better adjustability also improves quality control, as the quality of welding improves as well.
Featured Solutions
Product family
Flexlite GX product series contains welding guns to be used in MIG/MAG welding processes. All Flexlite GX welding guns enjoy the Flexlite features for user comfort, welding efficiency and extended consumable parts life. The GX family includes a wide range of welding gun models designed to serve specific welding needs.