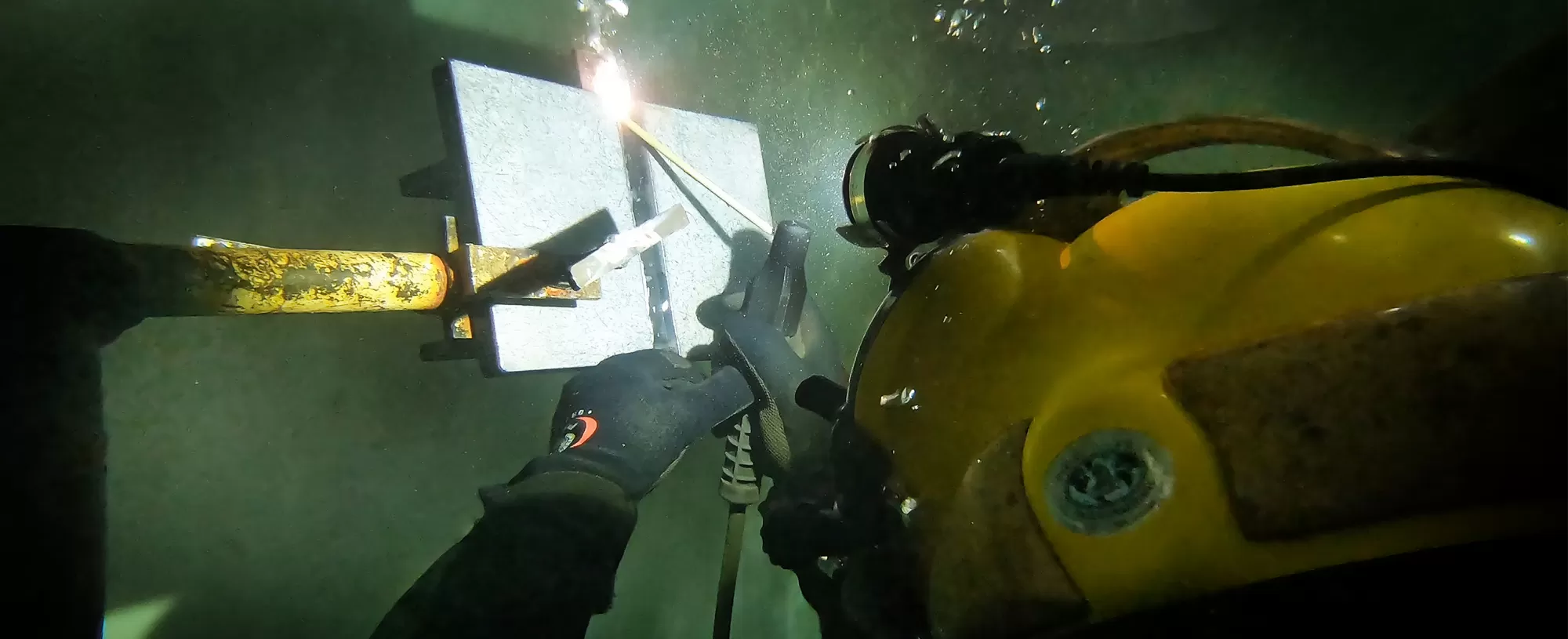
DG Diving Group
Underwater welding specialist
High-quality repair welding in exceptional conditions with Kemppi’s solutions
Empresa
DG Diving Group
Sitio web
dg.fiIndustria
Construcción naval
Ubicación
Turku, Finland
Material base
Ss, Fe
DG-Diving Group is known in the industry for its flexibility and good customer service. Their work consists of various underwater cleaning, maintenance, and repair work for the needs of the shipyard industry and shipping companies, and underwater welding is one of their most important working methods. Kemppi’s Master S perfectly suits their needs in underwater welding. Its compact size makes it easy to carry around, it has enough capacity, and the arc characteristics and adjustments are ideal.
DG-Diving Group is a Finnish company founded in 1983. The company currently employs 18 people in two units and is internationally acknowledged and trusted in its field. DG-Diving Group’s work consists of various underwater cleaning, maintenance, and repair work for the needs of the shipyard industry and shipping companies, and underwater welding is one of their most important working methods. DG-Diving Group's main operating area is Finland and the Baltic Sea regions, but the company has participated in numerous global projects in the Persian Gulf, West Africa, and Canada. The company has annual contracts, for instance, with the largest Finnish shipping companies.
Among the most common work tasks is regular hull cleaning; a cleaned ship consumes significantly less fuel. Removing a rope stuck to the ship’s propeller is also a very familiar task, as well as repairing and cleaning small oil leaks. In addition to smaller jobs, the company participates worldwide in emergency repair projects at sea, for example, caused by accidents. Repair work on ships requires special approvals.
DG-Diving Group has the approval of several international classification bodies, e.g., Det Norske Veritas, Bureau Veritas, Lloyd's, as well as Japanese and Korean approvals. DG-Diving Group prepares reports and documentation with detailed photos for all its work. The company also has the required environmental permits in its most important operating areas.
Challenging working conditions
Underwater welding is used for workpieces located below the water surface and cannot easily be moved to land due to their size or location. Underwater welding is mainly repair welding, and it is divided into wet welding and dry welding.
Wet welding is always performed as stick welding. The welder works under the surface wearing diving equipment, the welding spot being in direct contact with the water. In addition to a compact and portable stick welding machine, wet welding requires an insulated electrode holder to avoid electric shocks and special varnished welding sticks. The stick must not get wet before meeting the arc. The small size of the electrode holder is an advantage because the welding positions are often challenging, and the space is limited.
If the quality requirements of the weld are particularly high and the work is extensive, underwater welding can also be carried out as dry welding. In dry welding, the underwater welding spot is isolated from water with a special sealable dry space or chamber. The dry space is drained of water, filled with gas, and welding is performed inside the ship to be repaired. With dry welding, the weld’s quality characteristics can reach the same level as when welding on land.
Underwater welding is significantly slower than welding on land; a routine task that can be done in fifteen minutes on land can take up to an hour underwater. This is primarily due to poor visibility - working underwater requires significantly more precision. Therefore, dry welding is often preferred if the conditions and the task allow it. In wet welding, depth limits also come into play; underwater welding can be done at a depth of up to 30 m, but in reality, one rarely dives deeper than 10 m. At depths over 10 m, the diving time limits rising from higher water pressure make the work exceptionally challenging. There is always only one welder underwater at a time, and the work is done in one dive whenever possible. Depending on the task, the welder can take a break, and the other will continue.
Water properties also matter; in cold waters, the welder must dress more warmly. The salinity of the water, on the other hand, affects the flow of electricity; the saltier the water, the lower the current can be adjusted. The welder must, therefore, know his work environment.
Always prepared – good service is the key
DG-Diving Group is known in the industry for its flexibility and good customer service. The telephone emergency service works around the clock, and the repair team must be on the way to the destination within two hours after the call - the time is precisely defined in the annual contracts. Good service is the cornerstone of the company's operations; they are trusted and have repeatedly proven themselves worthy of that trust.
”Good and reliable service is what we offer. We say things as they are and get the work done as agreed. That is the core of our work”, said the company founder, Mauri Kalliomäki.
The company has a wide range of equipment; 12 fully equipped vans are waiting in the garage in Turku, always ready for a new task. In addition, DG-Diving Group has a lot of different equipment for measuring, cleaning, or repairing work. The company has produced most of their equipment and patented them. When the work takes place in Europe, the team usually drives to the destination with all the equipment; for more distant destinations, diving equipment is rented, and the company’s tools are sent to the site. Although the team is experienced, the tasks often surprise.
"Nearly every time, we have to apply our knowledge and develop new ways of working. Although we thoroughly think in advance how to best perform the task, the final assessment is only made on the spot, task-specific", said diving supervisor Simon Randström.

Underwater welding is done in harsh conditions and requires expertise from the welder. The welder works under the surface wearing diving equipment, and the welding spot is in direct contact with the water.

DG-Diving Group uses Kemppi Master S 500 for underwater welding because it is easy to carry around and has enough capacity.
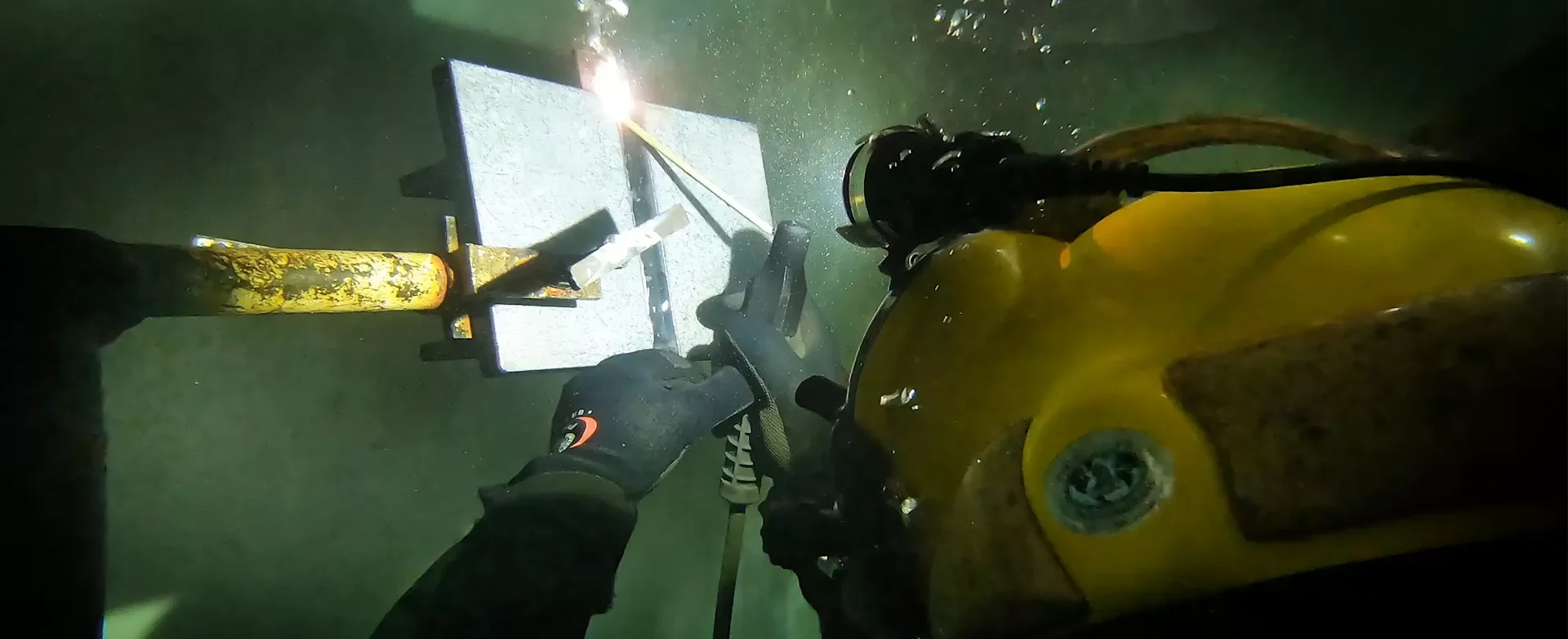
In underwater welding, there is always only one welder underwater at a time, and the work is done in one dive whenever possible.

Underwater welding is always performed as stick welding. Materials DG-Diving Group welds underwater are Fe and stainless steel.
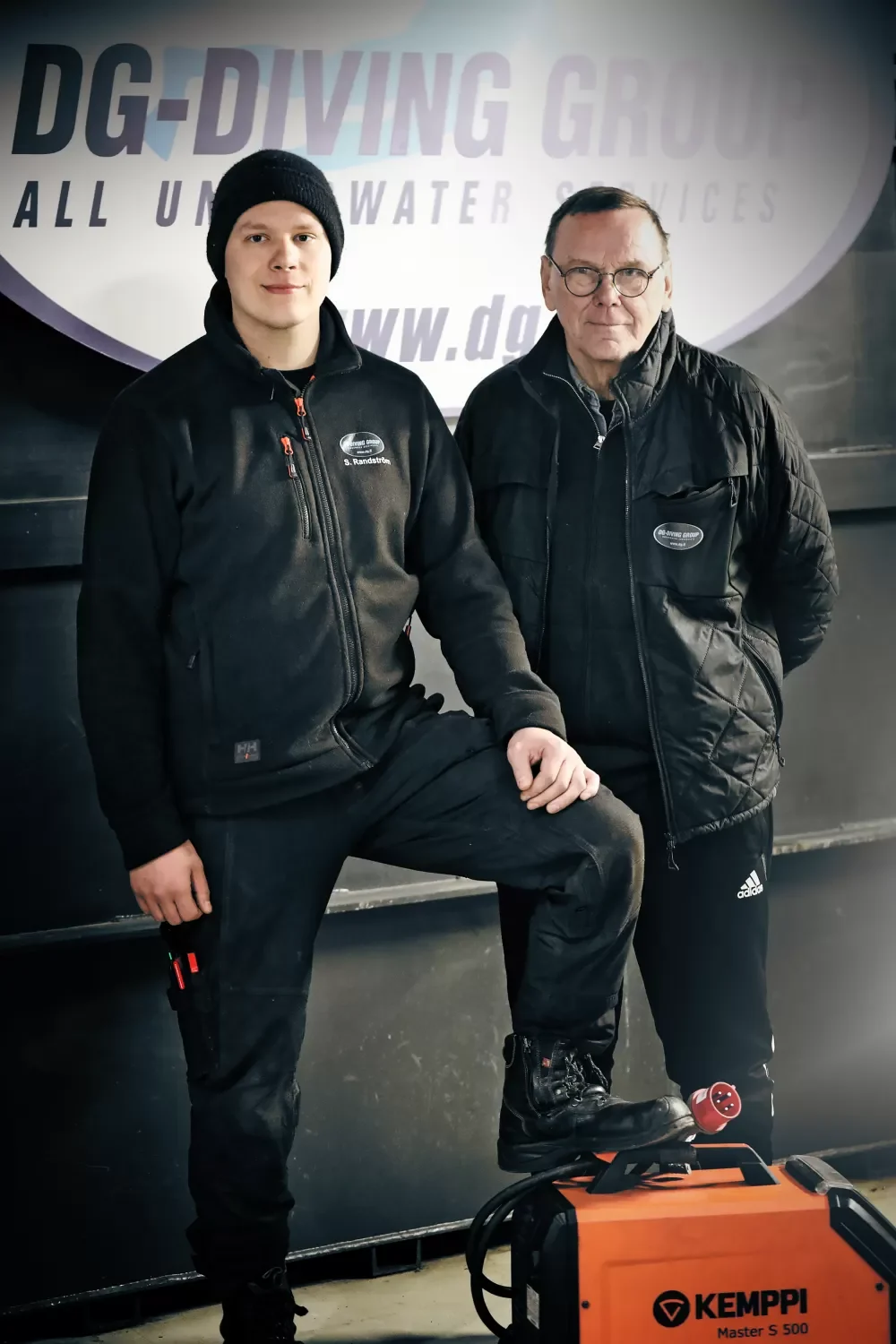
Simon Randström (left) and Mauri Kalliomaki (right) are happy with the cooperation with Kemppi and Master S welding machine’s capabilities in underwater welding.
Kemppi's Master S is a trusted partner for a stick welder
DG-Diving Group has always used Kemppi’s welding equipment, and currently, only Master S is used for underwater welding. Master S series MMA power sources are designed for high-performance professional welding, offering compact, robust, and portable MMA power solutions with optimum energy efficiency. A perfect partner for heavy-duty MMA welding where ease of use, reliability, and durability are paramount.
The powerful 400 or 500-amp power sources provide reliable welding results with efficient ignition. Suitable for use with a wide voltage network, Master S also integrates a Voltage Reduction Device (VRD) for increased safety at work.
"Master S suits perfectly for our needs, and its compact size makes it easy to carry around. It has enough capacity, and the arc characteristics and adjustments are ideal. A smaller machine might not have enough capacity to keep the arc burning throughout the task. A compact and reliable basic machine is the best option for underwater welding", said Randström.
In addition, the workshop has other Kemppi welding machines suitable for TIG and MIG/MAG welding. These machines are used for welding on-site and for the company’s own repair and manufacturing work. The workshop welds various materials, such as stainless steel and aluminum.
Kalliomäki and Randström are satisfied with Kemppi's cooperation; the customer service is good, and the delivery times are short. Master S has previously been specially tailored to meet the needs of underwater welding.
Featured Solutions
Familia de productos
La Master S está diseñada para la soldadura de varilla (MMA) de alto rendimiento. La fuente de potencia, que incluye la función de soldadura con electrodos celulósicos, ofrece unos resultados de soldadura excelentes con una experiencia de soldadura agradable.