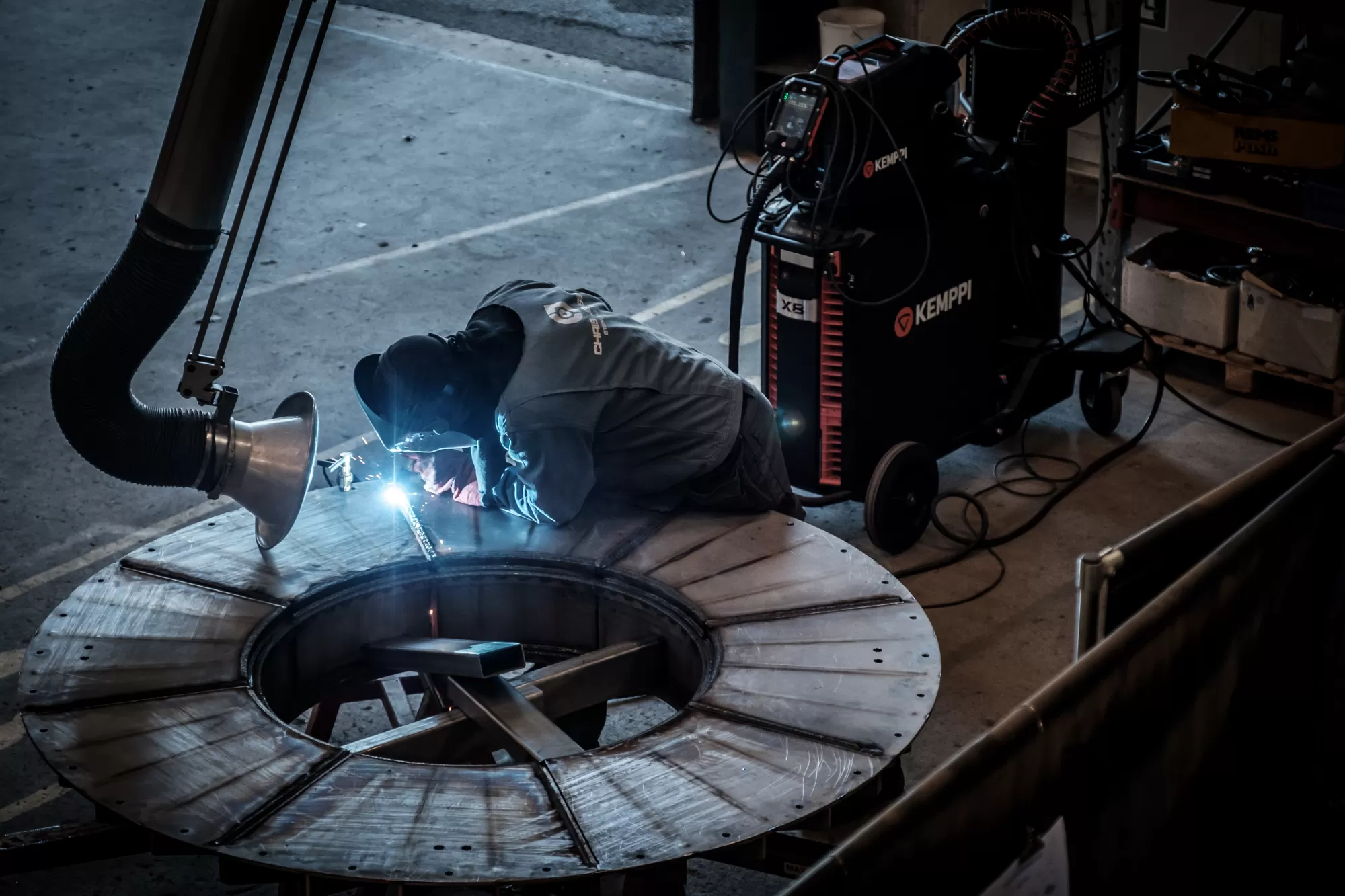
Chris Jensen
Expertos en fabricación con acero inoxidable
Sustitución de la soldadura TIG con la Kemppi X8 MIG Welder
Empresa
Chris Jensen
Sitio web
cjss.asIndustria
Fabricación de maquinaria
Ubicación
Stenlille, Denmark
Material base
Ss
Sin renunciar a la calidad de la soldadura, el fabricante a medida danés Chris Jensen A/S quiso probar la soldadura MIG, más productiva, para sustituir parcialmente la soldadura TIG. El funcionamiento rápido y sin salpicaduras de la X8 MIG Welder de Kemppi con WiseFusion fue un elemento clave de su exitosa transición.
Chris Jensen A/S produce maquinaria de máxima calidad y demás tecnología de producción para sus clientes en todo el mundo, por ejemplo, en las industrias petrolífera, química, farmacéutica y alimentaria. La empresa suelda y mecaniza principalmente acero inoxidable en sus unidades de producción en Stenlille, Slagelse y Kalundborg. También se encargan de ensamblar la maquinaria en las instalaciones de producción de sus clientes por todo el mundo.Como los requisitos de calidad de los clientes son muy exigentes, no permiten ninguna salpicadura ni el rectificado de las soldaduras. Así, los soldadores solían utilizar sobre todo equipos TIG para producir una soldadura perfecta.«Nuestra ventaja competitiva es, dicho en una palabra, calidad. Nuestros soldadores son muy hábiles y son capaces de enfrentarse a los retos de cualquier tipo de material, espesor y norma de calidad», afirma el gerente de Producción Allan Guldborg.
Una demanda creciente requiere productividad
Para ser capaz de responder a la creciente demanda y seguir siendo competitivo en un mercado cada vez más exigente, Chris Jensen quiere acelerar los procesos de producción siempre que sea posible, pero sin renunciar a la calidad. Alrededor del 90 % de la producción de Chris Jensen utiliza el proceso de soldadura TIG, que produce soldaduras de primera calidad, pero es más lento que otros procesos de soldadura con arco.
La transición a un proceso de soldadura más rápido sería una forma de aumentar la productividad de la soldadura y, en ciertas aplicaciones, la soldadura TIG podría sustituirse por la MIG. No obstante, esto exige mucho al equipo de soldadura, que tiene que estar precisamente a la altura de las expectativas de calidad que tienen los clientes.
«Si podemos convencer a nuestros clientes, que siempre han confiado en la soldadura TIG, de que podemos soldar con exactamente la misma calidad con MIG, pero más rápido, hay mucho potencial», nos explica Allan Guldborg.
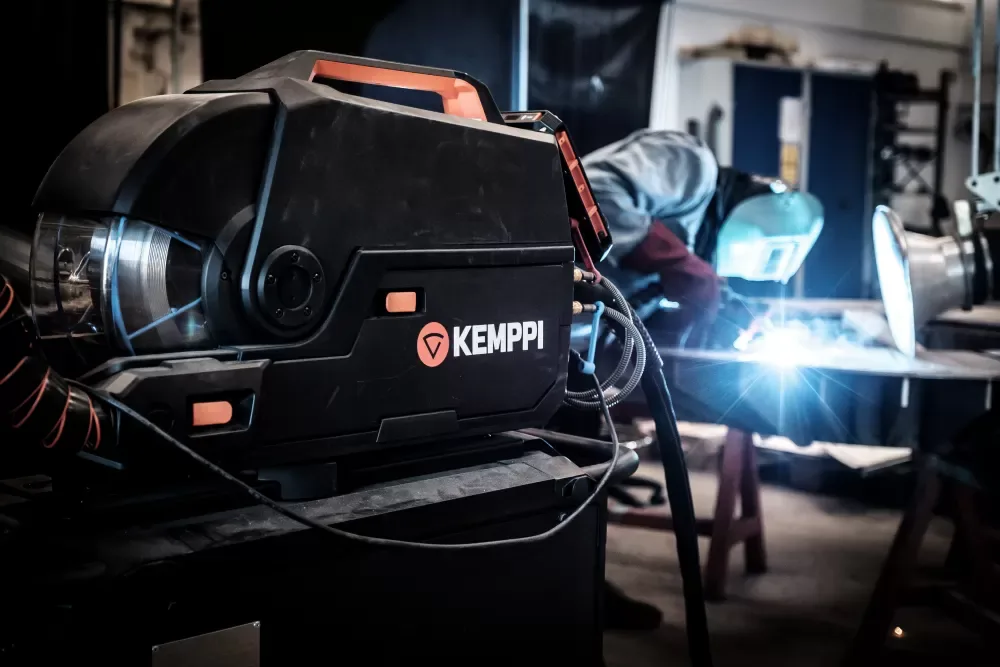
X8 MIG Welder y WiseFusion han sido elementos fundamentales en la exitosa transición de la soldadura TIG a la MIG.
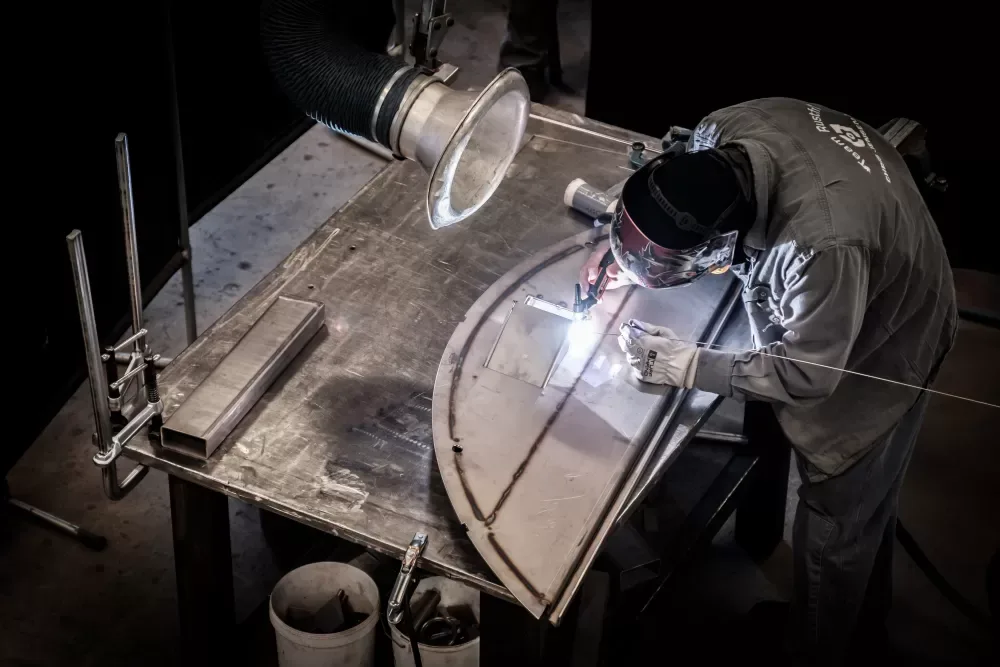
Alrededor del 90% de la producción de Chris Jensen utiliza el proceso de soldadura TIG.
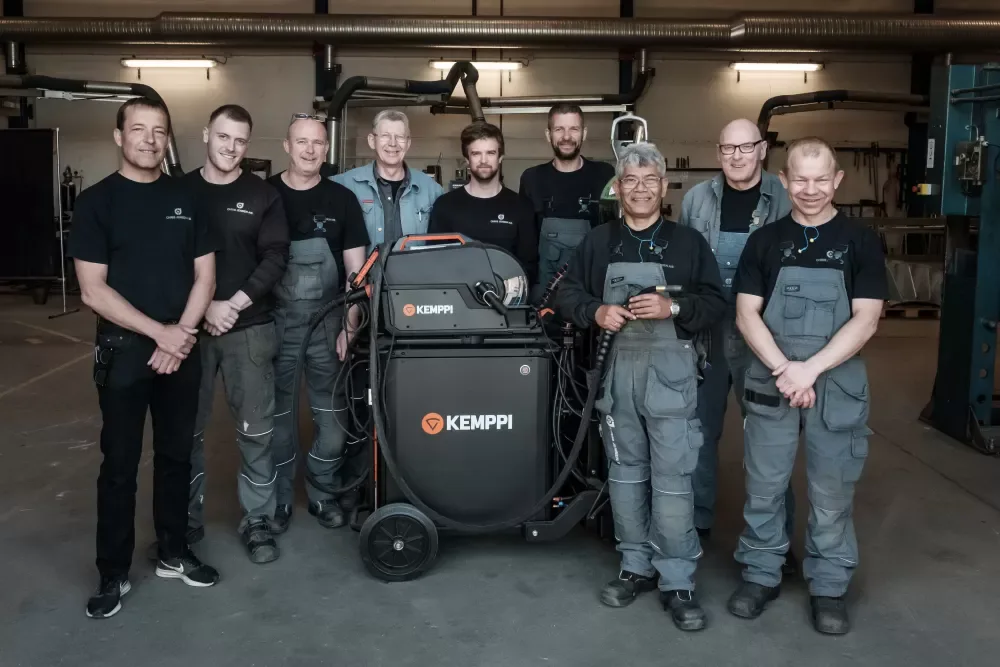
Los soldadores de Chris Jensen pueden hacer frente a los retos que plantean todo tipo de materiales, espesores y normas de calidad.
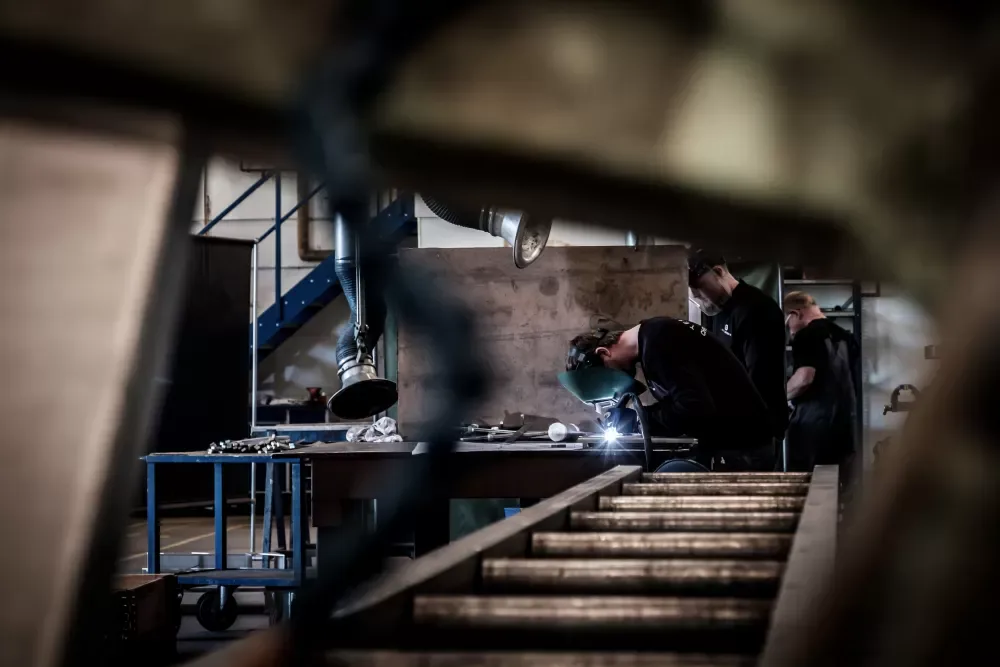
La empresa fabrica maquinaria de alta calidad y otras tecnologías de producción para sus clientes de todo el mundo.
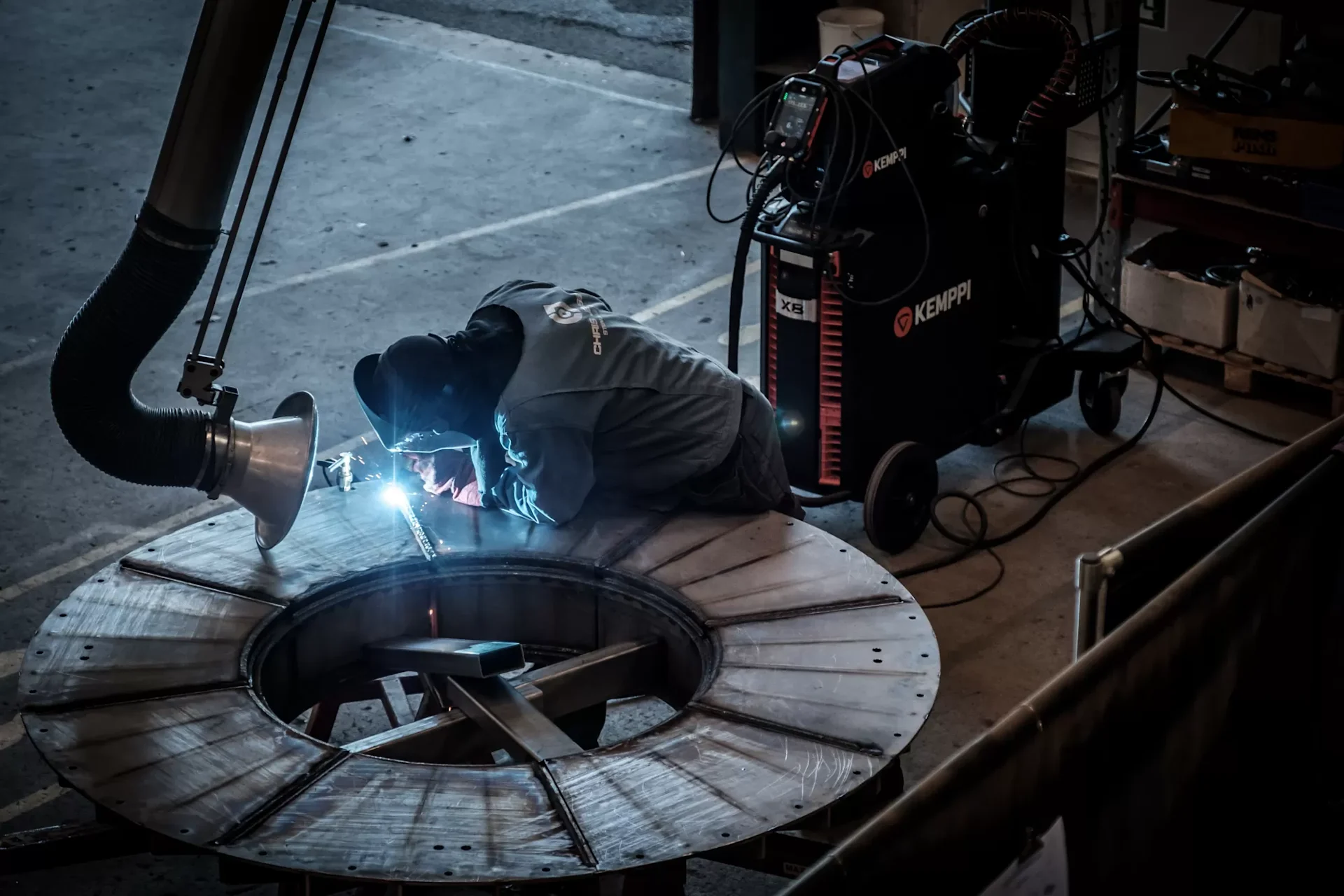
La velocidad de soldadura ha aumentado entre un 20 y un 30% en aquellas aplicaciones en las que se ha pasado de la soldadura TIG a la MIG.
Paso de la soldadura TIG a la MIG
Para Chris Jensen, el funcionamiento rápido y sin salpicaduras de la X8 MIG Welder de Kemppi con el proceso especial WiseFusion fue un elemento clave de su exitosa transición. Se trata de la última incorporación a la flota de soldadura de la empresa, que comprende únicamente equipos de soldadura TIG y MIG de Kemppi. Según Allan Guldborg, la X8 MIG Welder es fácil de usar y su interfaz de usuario inalámbrica, Control Pad, atrae especialmente a la generación más joven de soldadores profesionales.
En la práctica, la X8 MIG Welder ha sustituido el proceso de soldadura TIG en algunas de las aplicaciones de soldadura con espesores de material de 5 mm o más.
«Durante los últimos dos meses, la velocidad de soldadura ha aumentado de un 20 a un 30 % en dichas aplicaciones que hemos cambiado de TIG a MIG. Las soldaduras han sido bellas y sin salpicaduras. No obstante, el cambio a MIG no es posible en todas las aplicaciones.»
La cooperación de Chris Jensen con Kemppi se remonta a varias décadas.
«Llevamos trabajando con Kemppi más de 40 años. Sus máquinas son muy estables y fiables. Cuando es necesario, su red de servicio global ofrece una asistencia excelente tanto en Dinamarca como adondequiera que nuestros soldadores lleven sus equipos para hacer trabajos de ensambl
Featured Solutions
Familia de productos
La serie de productos Flexlite GX comprende pistolas de soldar para procesos de soldadura MIG/MAG. Todas las pistolas de soldar Flexlite GX disfrutan las características de Flexlite en cuanto a comodidad, eficiencia de soldadura y larga duración de consumibles. La familia GX incluye una amplia gama de modelos de pistola de soldar diseñados para satisfacer necesidades de soldadura concretas.
Familia de productos
La función optimizada de soldadura WiseFusion produce un arco muy estrecho y con una alta densidad energética que agiliza la soldadura y disminuye la entrada de calor.