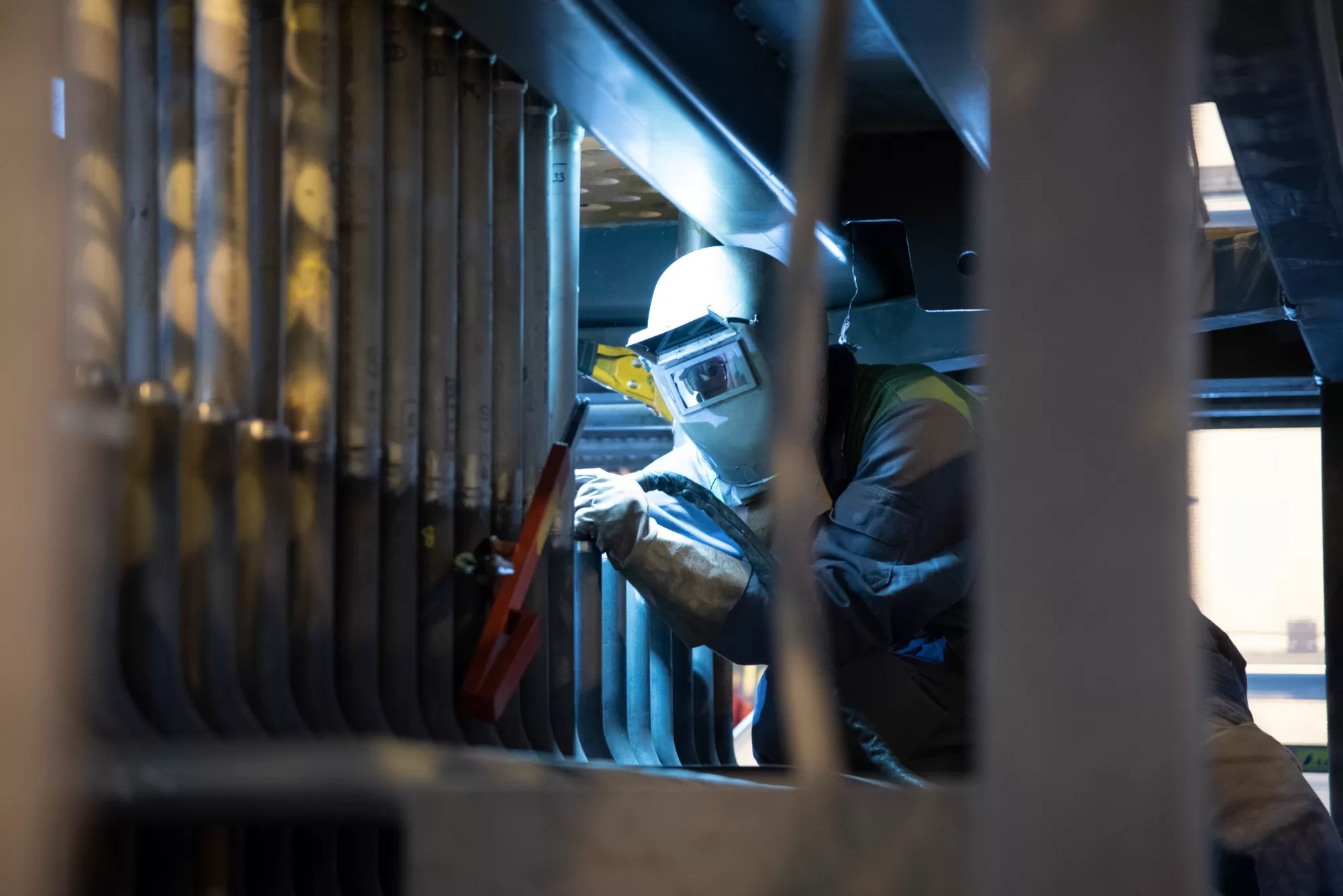
Valmet
Leading supplier to pulp, paper and energy industries
Demanding welding of boilers with Kemppi MasterTig
Valmet’s welders must produce flawless welds in tight spaces inside welded structures with ever-changing base materials. Valmet and Kemppi have long collaborated to overcome the welding challenges set by the base materials. The most recent example of the tight-knit partnership has been the successful testing of the new MasterTig.
Valmet’s workshop in Tampere, Finland produces boiler pressure parts for energy and recovery boilers. A part of Valmet’s Pulp and Energy business line, the unit employs about 100 people of whom roughly 75 are welders. The workshop focuses on components that are either critical to the boiler’s operation or contain challenging base materials or structures.Only a handful of manufacturers in the world can supply as broad selection of boilers in this size range as Valmet. Most of the production is exported, as the demand for sustainable solutions and drive to stop using fossil fuels is constantly increasing. Valmet’s strengths in this market are its versatile product range and the ability to deploy a wide selection of biofuels. Service operations, including boiler inspections, maintenance, repairs, modernizations, and upgrades, are also an important part of the business.
Quality and base materials as biggest challenges
The high pressures and temperatures of boilers require flawless welds. Senior Manager, Production Ville Lehtikangas explains that each weld is subject to various inspections and has a predetermined and validated welding process. Similarly, the welders must be qualified for the welding process, filler material and material pair at hand. Quality control takes up roughly 10% of total work hours.
The welders process stainless steel, carbon steel, and dissimilar metal joints. New base materials and solutions are introduced constantly, and the variety of alloys in e.g. stainless steel is huge.
“Special materials are needed because the boiler welds must endure over 150 bars of pressure at high, over 500 °C temperatures. High corrosion and erosion resistance are also required. For example, circulating fluidized bed superheaters inside the Loop Seal collect every last bit of heat energy from the sand circulating in the furnace and are practically undergoing continuous sandblasting,” Lehtikangas says.
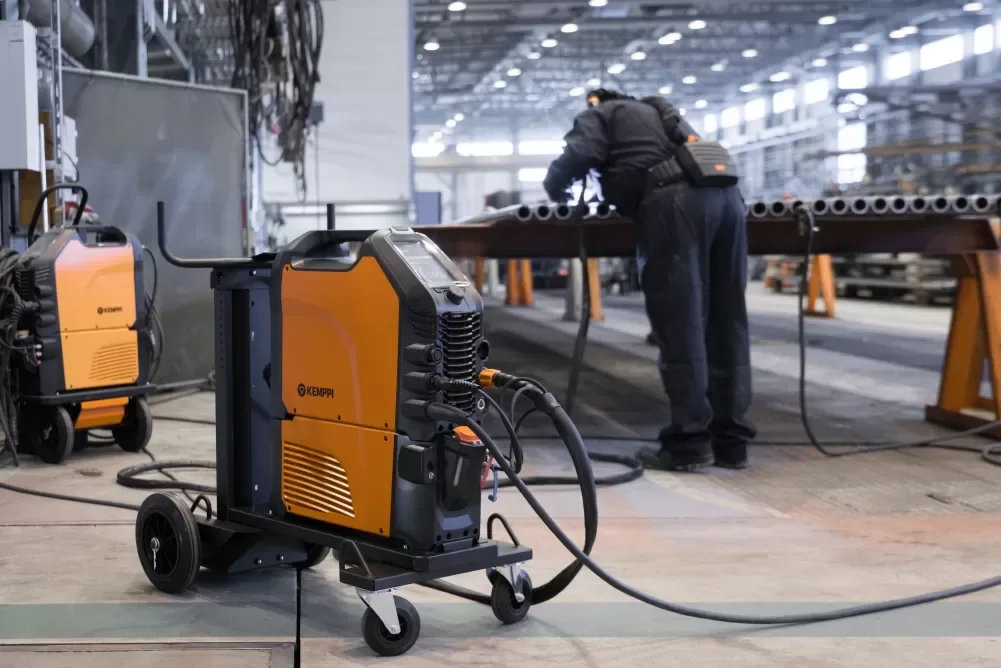
Valmet’s workshop in Tampere, Finland produces boiler pressure parts for energy and recovery boilers.
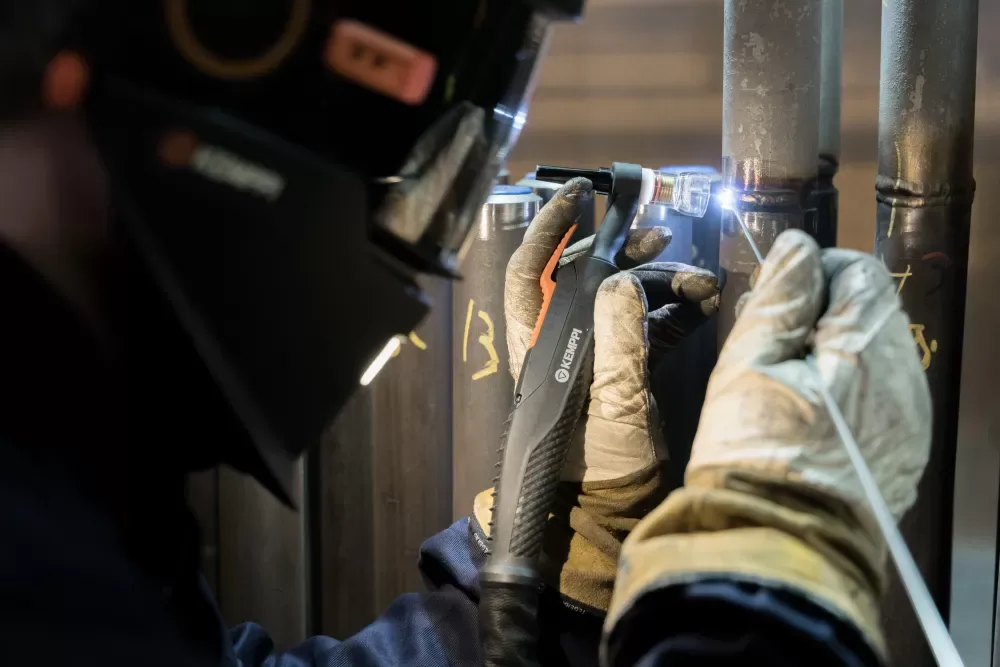
The welders have been satisfied with the new Flexlite TX TIG torches’ design and wide selection of consumables.
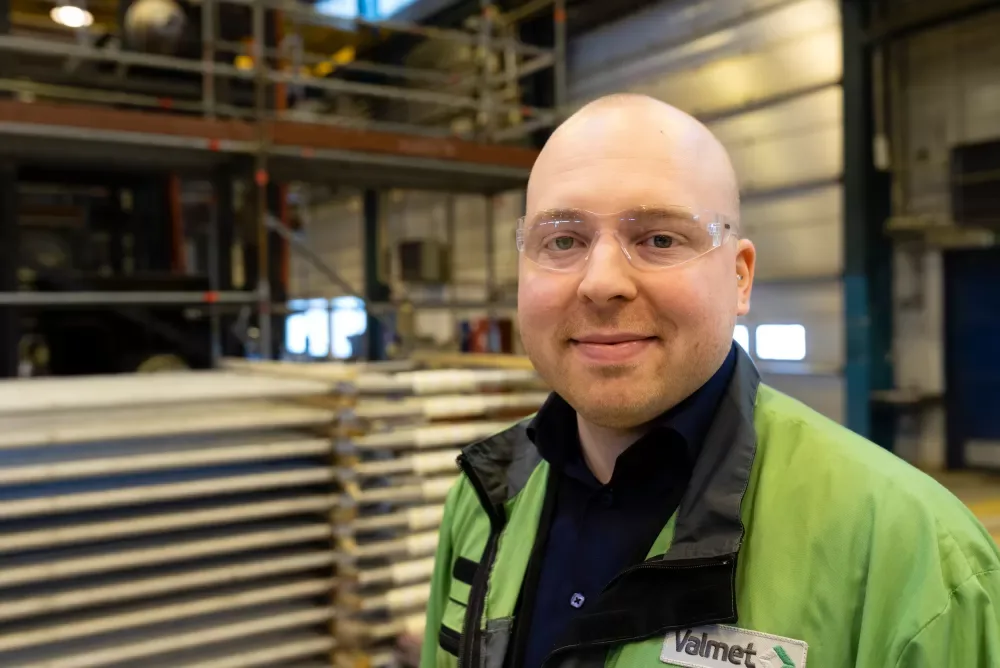
Senior Manager, Production Ville Lehtikangas appreciates the support from Kemppi in solving welding challenges.
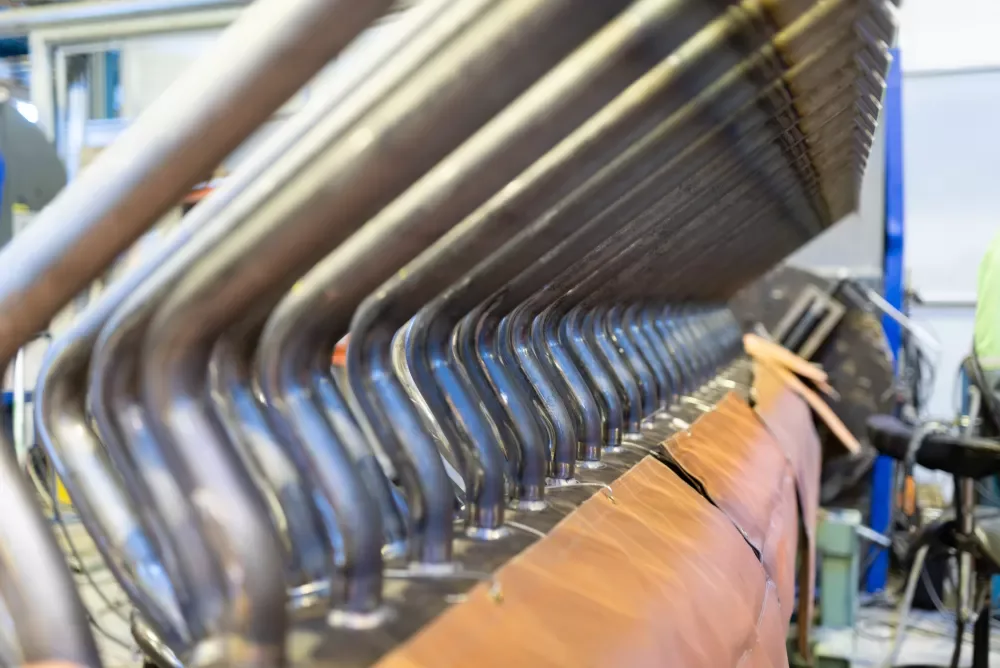
The welds in the boilers must endure over 150 bars of pressure at high, over 500 °C temperatures.
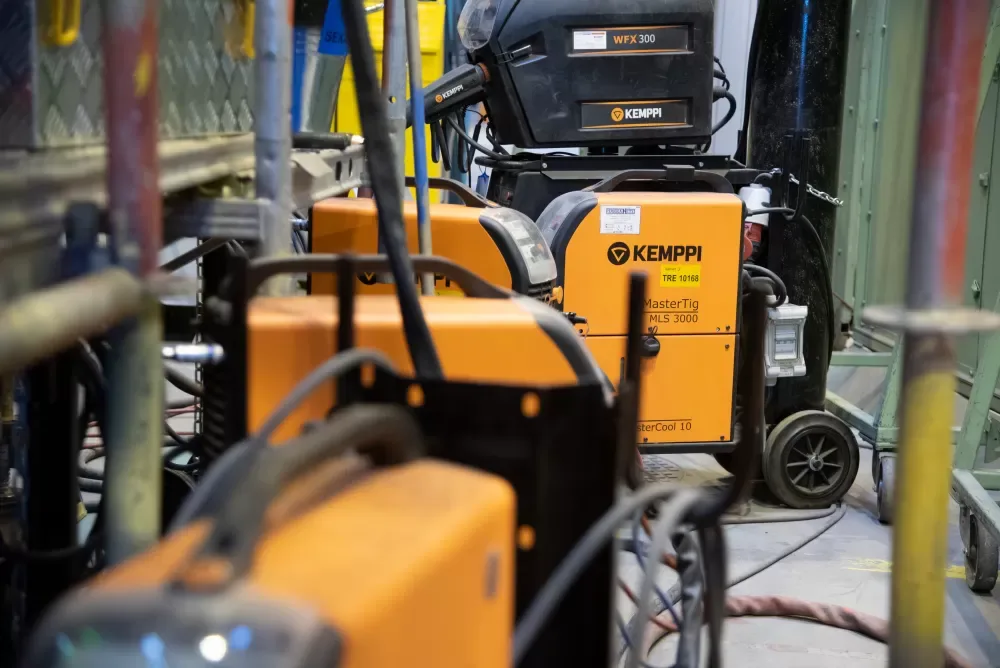
A vast majority of Valmet’s welding fleet at Tampere is made by Kemppi.
Added value with cooperation
A vast majority of Valmet’s welding fleet at Tampere is made by Kemppi. The long-term cooperation has only become tighter over the past couple of years.
“For us, it is crucial that Kemppi’s experts guide and support us when needed, and that we have the opportunity to solve any surfacing welding challenges together,” Lehtikangas says. “We are engaged in a continuous discussion. We tell Kemppi specialists what kind of new materials and welding parameters we have planned to use and based on their knowledge, they give their suggestions that we can try out. I hope that our cooperation will continue as fruitful as it has been and that it will deepen even further according to our principle of continuous improvement.”
The endurance test of the new generation MasterTig is an excellent example of the tight-knit partnership. A six-month test use period during winter and spring 2019 offered a good overview of the welding equipment’s suitability for Valmet and sorted out any teething troubles with the new product.
According to Welding Coordinator Simo Lustig, Valmet’s welders consider the new MasterTig as comparable to the previous generation of high-quality TIG welding equipment, MasterTIG MLS 3000. “They have especially praised the improved stick welding properties. The usability has also gotten better. For example, the new torch is narrower and easier to handle, and the selection of consumables is wider.
Lustig has been working as a welding coordinator for seven years. He finalizes welding procedure specifications based on the given welding plan and pre-tested parameters. Due to his area of responsibility, he is in continuous contact with Kemppi.
“I have worked with Kemppi for as long as I can remember. We have always worked in the spirit of cooperation and received support whenever we have needed.”
Featured Solutions
Product family
Flexlite TX welding torches are designed to be used with Kemppi's TIG welding equipment. The torch range includes several neck models, offering superb cooling performance and good access to challenging joint designs.
Product family
The new master of AC and DC TIG welding, MasterTig sets new standards for weld quality, usability, and power efficiency. Its modular design ensures that your machine exactly meets your needs.