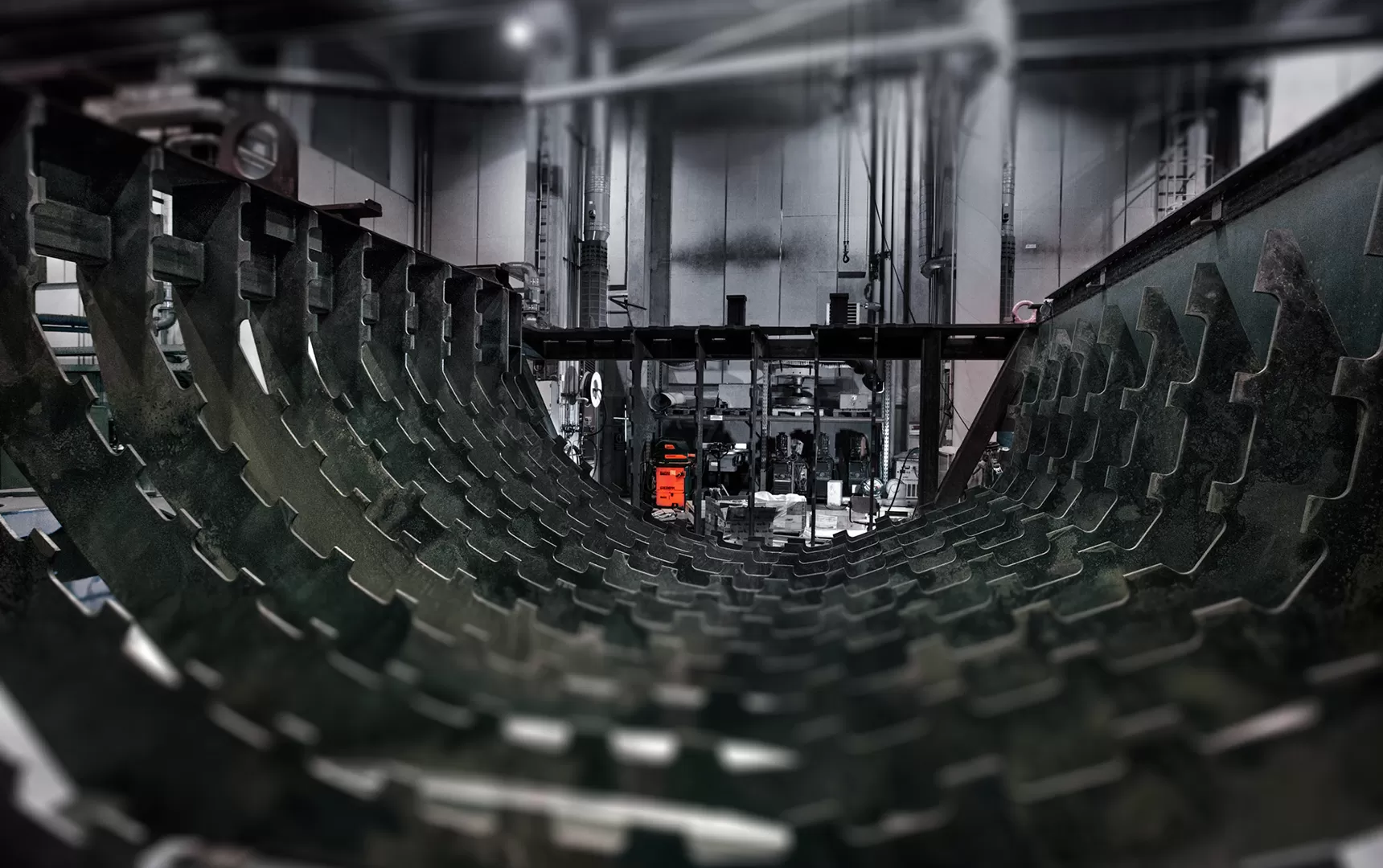
Outotec Turula
Global ledare inom anrikningsteknik
Når nya höjder med WeldEye, programvaran för svetskoordinering och dokumentation
Outotec Turula använde WeldEye för att effektivera sin svetskoordinering och sparade hundratals dokumentationstimmar varje år. Dokumenterade bevis på svetskvaliteten och efterlevnaden av kvalitetsstandarder stärkte dessutom företagets konkurrenskraft ytterligare.
Outotec Oyj är ett finskt högteknologiskt företag som specialiserar sig på att konstruera och utveckla skräddarsydda processmaskinlösningar och livscykeltjänster för gruv-, metall-, energi- och vattenindustrierna. Företaget, som har 4 800 anställda, verksamhet i 25 länder och affärsintressen i 80, är känt för innovativa produkter och lösningar som skapar mervärde av naturtillgångar åt kunden på det mest hållbara sättet.Av Outotecs fem produktionsanläggningar är Outotec Turula Oy den största fabriken, med 200 anställda och 25 000 m² i lokaler belägna i Outokumpu i Finland. I den mekaniska verkstaden i Turula tillverkas utrustning för metallurgiska processer, huvudsakligen kopparproduktion. Företaget har alltid investerat i den senaste tekniken för att säkerställa ett sammanhängande flöde i produktionsprocessen.
Främsta utmaningen
Outotec Turula, som har 70 MIG-/MAG-, TIG- och MMA-svetsmaskiner och 60 heltidsanställda svetsare, behövde en lösning som kunde vara till hjälp med att hantera det stora antalet svetsare, övervaka svetskvaliteten och förbättra svetsproduktiviteten överlag. Arbetet med krävande material gjorde det mycket viktigt att hålla sig inom WPS-gränserna. Dessutom var konkurrenskraften direkt kopplad till förmågan att konsekvent uppfylla kvalitetskrav. Under produktionens högsäsonger var man dessutom tvungen att anställa extra personal, vilket fick uppgiften med att hantera svetskvalitet och svetsarkvalifikationer att framstå som omöjlig utan ett ordentligt system på plats.
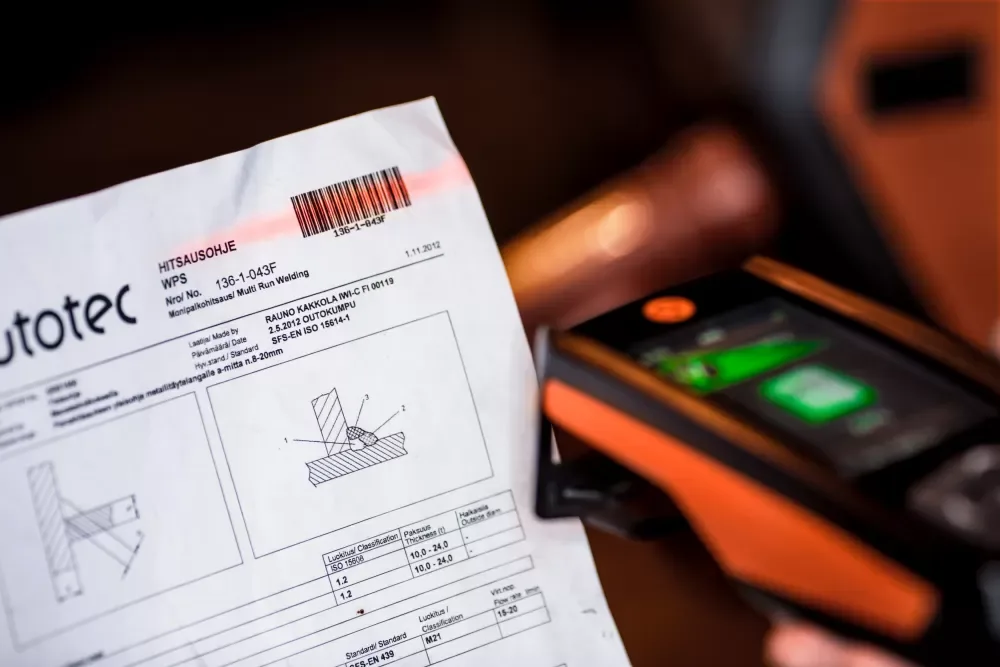
Smart Reader läser in en specifikation för en svetsprocedur.
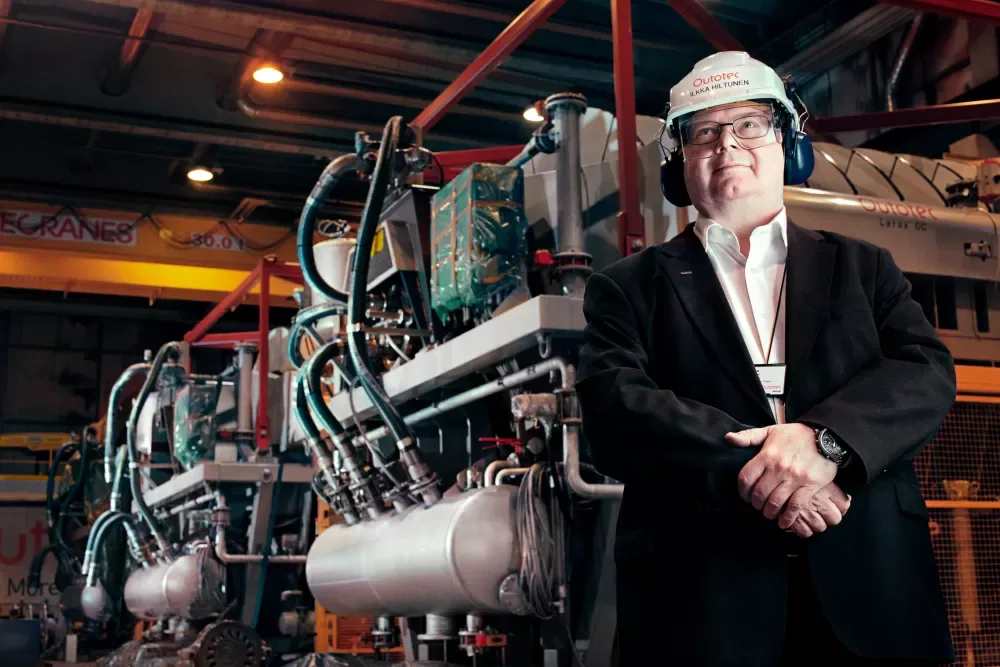
Senior Advisor Ilkka Hiltunen med tre robusta skivfilter som ska skickas till Brasilien.
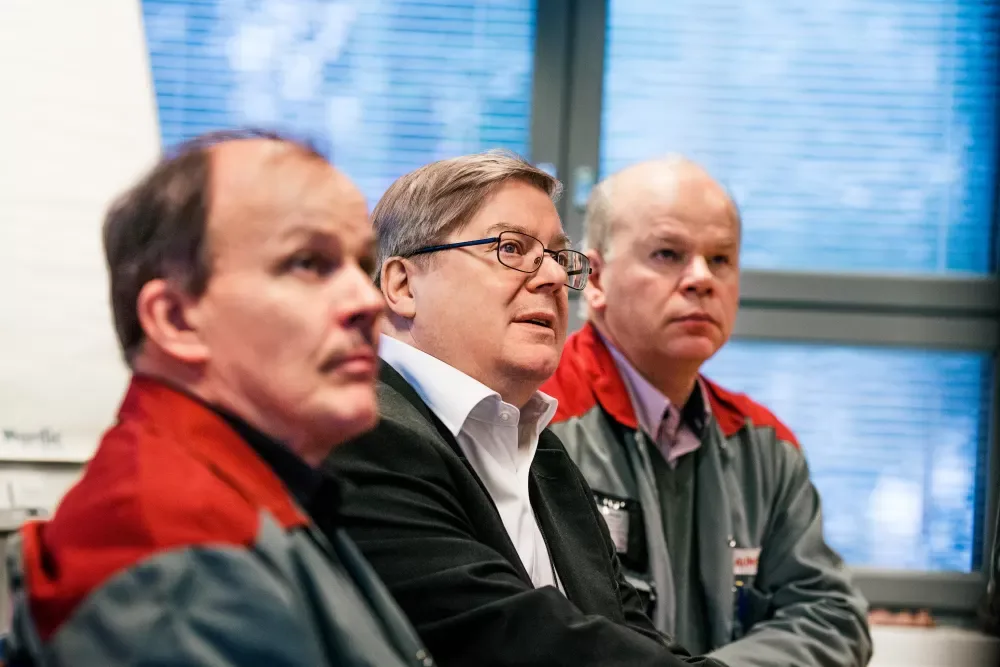
Kari Koistinen, Ilkka Hiltunen och Rauno Kakkola från Outotec Turula.
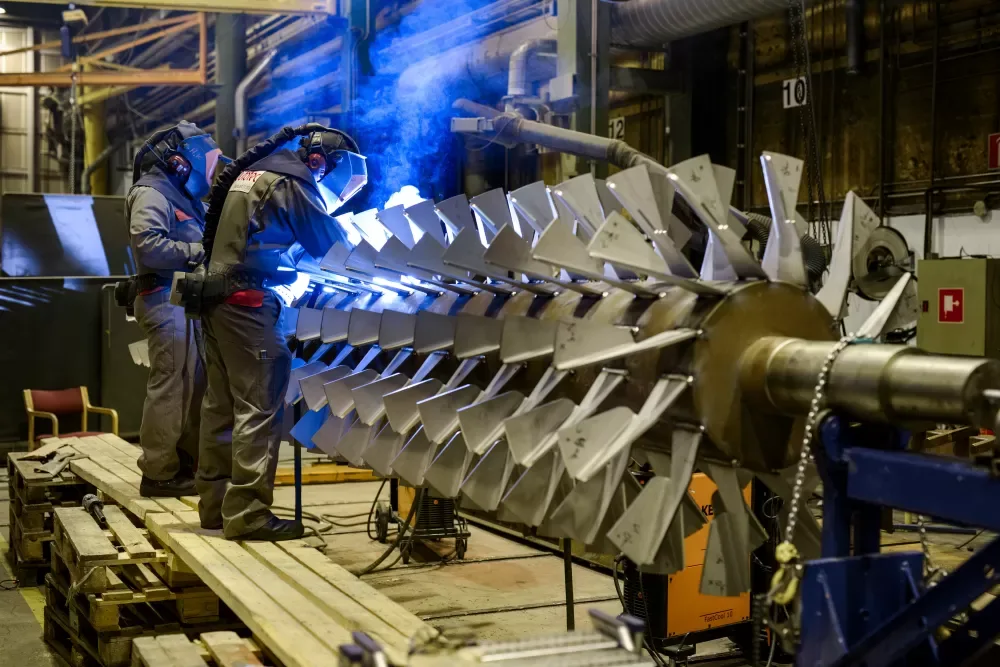
Pågående arbete i Outotecs verkstad i Turula.
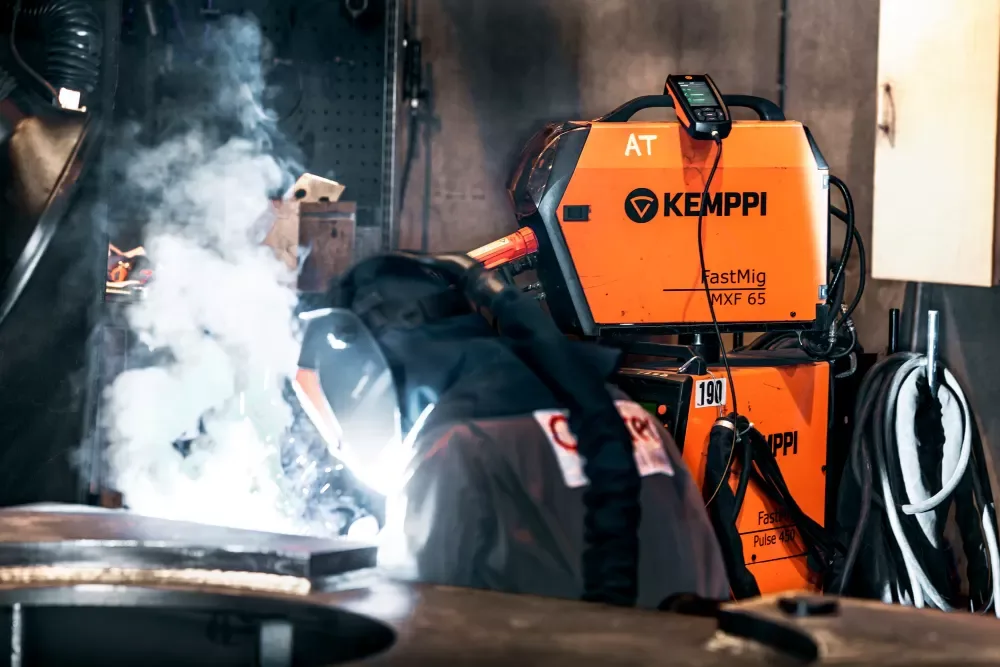
Programvarulösningen för svetshantering används i Outotec Turulas svetsproduktion.
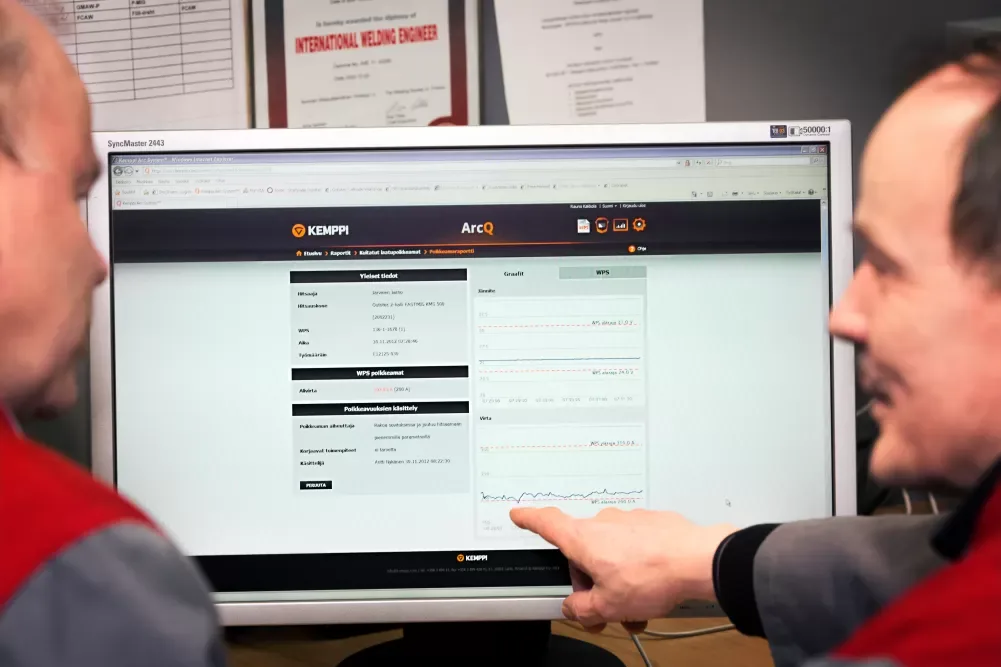
Rauno Kakkola och Kari Koistinen analyserar en avvikelserapport om programvarans användargränssnitt.
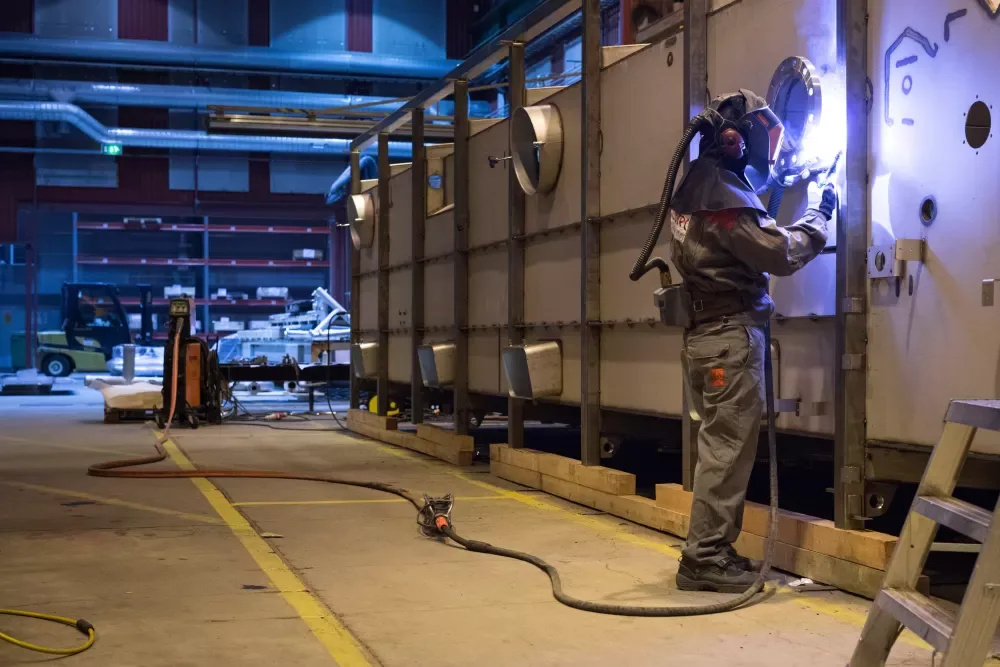
Kemppi SuperSnake i arbete.
Kemppis lösning
Outotec har utvecklat sitt partnersamarbete med Kemppi genom att införa olika moduler av WeldEye, programvaran för svetskoordinering och dokumentation (tidigare kallad KAS 3), i faser. Kemppi försåg 2012 verkstaden i Turula med ARC Quality (numera tillgänglig som WeldEye Quality Control) som en konkret metod för att bekräfta svetskvalitet. Med ökande krav på kvalitetssäkring från kunder i hela världen betraktades programvarans förmåga att producera data och rapporter om svetskvalitet som en klar konkurrensfördel. Dessutom kunde Outotec nu enkelt visa att svetsproduktionen uppfyllde kvalitetsstandarden EN ISO 3834-2 i regelbundna granskningsförfaranden.
Under 2014 uppgraderade Outotec Turula till den kompletta programvaran för svetskoordinering och dokumentation. Denna täcker verkstadens svetsarbeten i alla avseenden. Nu blev det inte bara möjligt att kontrollera och bekräfta svetskvalitet på toppnivå. Hanteringen av WPS och svetsarkvalifikationer effektiviserades även, och hela projektets dokumentation kunde färdigställas på bara några minuter.
Efter dessa positiva erfarenheter och bevisade fördelar överväger Outotec nu att utöka programvarulösningen till att omfatta deras andra produktionsanläggningar och även underleverantörer. WeldEye är en modern och molnbaserad lösning som är perfekt för ett globalt verksamt företag som Outotec, som har behov av en svetskoordineringslösning för flera platser.
Featured Solutions
Produktfamilj
WeldEye är en universallösning för koordinering av svetsproduktion.